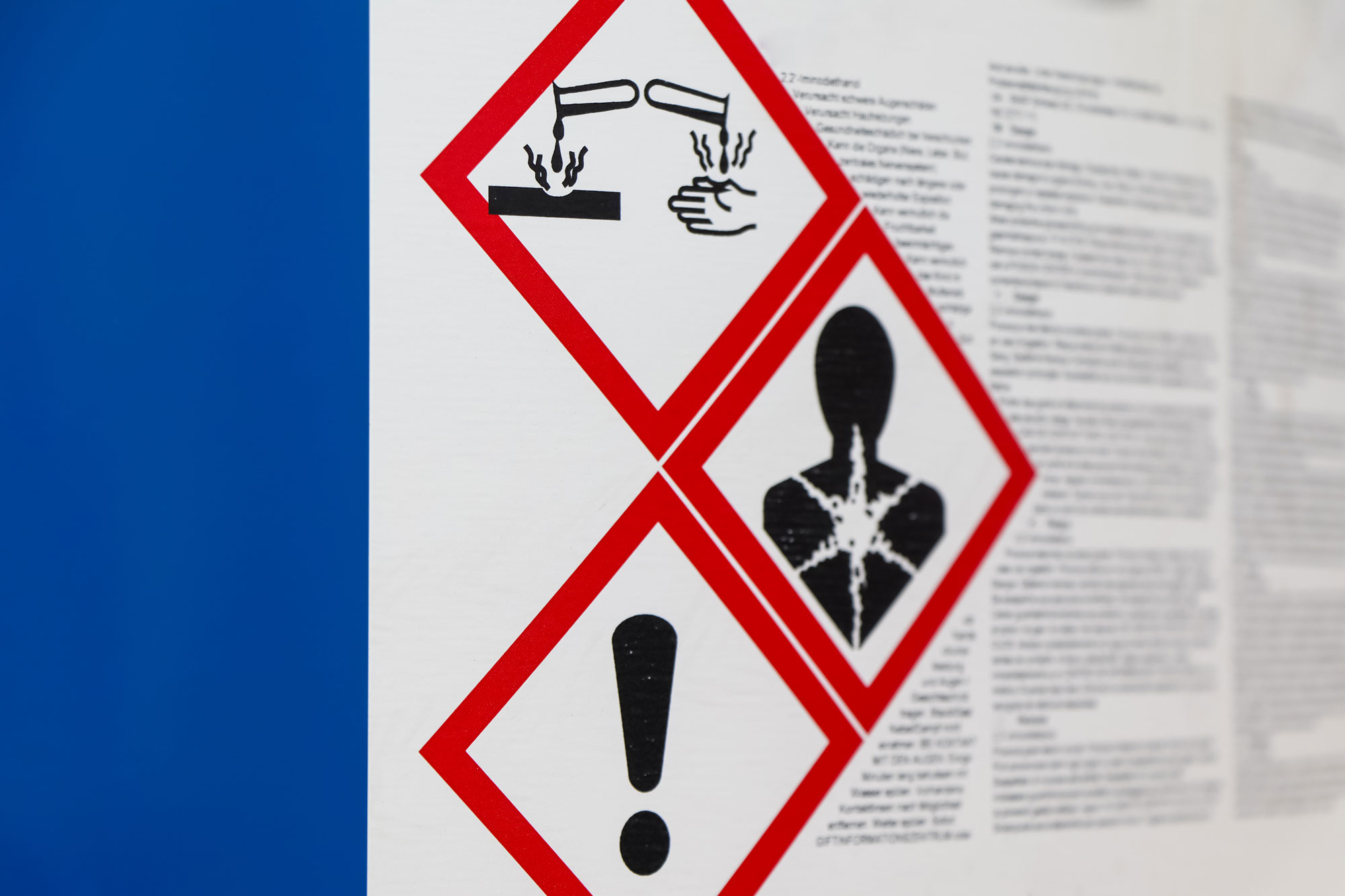
CoSHH: six simple steps towards compliance
Published Apr 28, 2021
The Control of Substances Hazardous to Health, or CoSHH as most people refer to it, is the primary set of regulations in the UK that govern the use of hazardous substances in the workplace. By law, CoSHH requires employers to conduct a formal risk assessment for any exposure to a hazardous substance that could occur in conjunction with their work. Hazardous substances can cause a wide variety of injuries and ill health effects, from mild irritation to corrosive burns, and even long-term illnesses such as cancers. CoSHH is designed to ensure that exposure to these substances is controlled and does not lead to worker ill-health.
Hazardous substances can often be daunting for many people, but you don’t need a chemistry degree to manage CoSHH effectively! We recommend the following six steps to help secure your CoSHH compliance and we can provide several training and consultancy options to your organisation to support you.
Step 1 – Identify substances and eliminate where possible
The first step is simple – identify the substances that are subject to the CoSHH regulations and those that are not.
What CosHH covers:
- Purchased products – paints, adhesives
- Process emissions – dusts, welding fumes
- Biological material – animal waste, viruses
- Contaminants – used engine oils
Some notable substances do not fall under CoSHH regulations but will have their own set of regulations for their governance; examples of which include asbestos, lead and radioactive materials.
Controlling exposure:
CoSHH covers exposure to a substance - if you are not exposed to the substance in the workplace then you do not need to have a CoSHH assessment for it. Once you have identified exposure to a hazardous substance, your first duty is to try and prevent the exposure. To support this, we recommend using the hierarchy of control.
Step 2 – Gather information
Once you are ready to compile a CoSHH risk assessment, you should ensure that you have all of the information that you need.
Safety Data Sheet (SDS):
If it is a manufactured product, the Safety Data Sheet (SDS) will outline the hazard information associated with that specific product. An SDS is not a CoSHH risk assessment, but simply a starting reference point as they will often only give information on the substance itself, not how to control its use or reflect how you use that product.
Exposure scenarios:
When you have the correct SDS or other information on the hazardous substance you must consider the way in which employees are being exposed:
- Method of use
- Area of use
- Length of exposure
- Quantities used
- Number of people exposed
- Frequency of use
Step 3 – Assess the risks and identify control measures
When carrying out a CoSHH risk assessment you should always be mindful of the two different types of risk they carry. Many substances can cause short-term (acute) damage, but a surprising number of substances can have long-term (chronic) effects after long periods of repeated exposure.
The CoSHH regulations put specific emphasis on the control of these types of substances as the potential outcomes can be irreversible. You should already have a form of health surveillance in place – check to see if you’re doing enough or whether you could do more!
Acute:
- Effects are immediate responses to short-term exposures
- Wide variation in effects from simple irritation to death
- Symptoms include irritation, nausea and burns
Chronic:
- Ill-health has a latency period and will often appear many years after exposure
- Develops from prolonged and / or repeated exposures
- Conditions include occupational asthma, dermatitis or different types of cancers
Step 4 – Record the CoSHH assessment
Organisations of five or more employees must record their risk assessments, but regardless of your size it’s still best practice to record your assessments – especially with something as serious as CoSHH! To support you, SSG does have a CoSHH template available to complete your own assessments but whatever template you decide to use, it should incorporate the following nine steps:
- Record all of the details of the hazardous substance you have collected
- Identify the hazards associated with using these substances by using the CLP hazard symbols (red diamond)
- List the occupational exposure limit; available from the SDS or HSE’s EH40 document
- Include how the substance is being used and in what type of working environment
- Determine the risk of using the substance and routes into the body to include appropriate controls
- Include emergency arrangements
- Include instructions on how to safely handle, store and dispose of the substance
- Consider additional actions such as additional controls, training, reducing quantities etc.
- Sign and date the document and establish when the next review will take place
Step 5 – Implement controls and train employees
Once the CoSHH risk assessment has been completed you must ensure that control measures are put in place. These will vary depending on the task, substance and exposure level. You may already be doing enough through the use of extraction, safe systems of work and PPE. However, you may need to do more such as air monitoring and additional health surveillance for employees.
Training employees:
Providing information, instruction, training and supervision to employees on risks to their health and safety is a duty of all employers. Once you’ve worked to create your CoSHH risk assessment, make sure employees know the contents and have additional training so that they know how to maintain the health and safety of themselves and others, make them feel protected and valued, protect your reputation, reduce likelihood of prosecution and fines and maximise your competitive edge.
Step 6 – Ongoing management and review
Now that you’ve got your CoSHH risk assessment(s) in place, don’t lose momentum! Employers have a duty to review all types of risk assessment, and CoSHH is exactly the same. You need to know that your control measures are still working and if you can do even more to reduce exposures to hazardous substances and further reduce the risk to your employees.
Typically, risk assessments are reviewed annually but you will also need to review them if a new SDS is published for the substance, a process changes, new technology is introduced, control measures fail, safer substitutes are found, employees suffer from health conditions when exposed, or if an accident or incident occurs.
The CoSHH cycle
Writing CoSHH risk assessments is just one part of successfully managing hazardous substances. The CoSHH cycle shows employers the steps they need to take to ensure all aspects of the CoSHH regulations are implemented.
Contact SSG about our full range of CoSHH services and to find out more about how the CoSHH cycle can be used in your organisation.
Source: David Wright